Mold Design and Demoulding of Rubber Products
Release time:
2022-11-29
The mold for rubber products must be easy to demould during design, accurately conform to the contour and shape of the rubber product, and the structure should be simple, reasonable, easy to operate, and meet the technical requirements;

1. Rubber product mold
(1) The mold for rubber products must be easy to demould during design, accurately conform to the contour and shape of the rubber product, and the structure should be simple, reasonable, easy to operate, and meet the technical requirements;
(2) The mold should be maintained frequently to observe its cleanliness, whether it is deformed, whether the positioning is firm, whether the surface is smooth, etc.
2. The structure of rubber products is unfavorable. When designing rubber products, attention should be paid to its shape, thickness, and demoulding slope, among which the demoulding slope is the main factor. After the product comes out of the oven, it will shrink centripetally due to the cooling of the product, which will generate a large clamping force on the core or pin, thus hindering demoulding. If the demoulding slope is increased, this resistance can be significantly reduced, and defects such as tearing of the product due to no slope can be avoided.
3. The product formula is unreasonable. The vulcanizing agent and accelerator in the formula are not enough, or the vulcanization temperature and time design are unreasonable, resulting in insufficient sulfur; or too much raw rubber content, too much accelerator vulcanizing agent, etc. will also cause difficulty in demoulding.
4. Production process In the production process of rubber molded products, injection pressure, holding pressure, vulcanization temperature, vulcanization time, etc. will also affect the difficulty of demoulding. For example, if the injection pressure is too high, it will cause elastic deformation of the mold parts and cause extrusion force. If the pressure holding injection force is too high and the time is too long, it will lead to an increase in the pressure in the mold cavity, resulting in greater internal stress, causing deformation of the mold parts or Flashing occurs between mating surfaces, making demoulding more difficult.
The second is the demoulding method. Through the analysis of the demoulding factors, we can use the following methods to avoid or solve the difficult problem of demoulding.
1. The structure of the mold is reasonable, and the rigidity of the mold should be improved as much as possible; the maintenance of the mold should be done in a timely manner, such as cleaning (electroplating, spraying PTFE, sandblasting), etc.
2. The structural design of rubber products should be easy to demould and have sufficient slope. 3. Choose a reasonable and appropriate viscosity formula. Properly adjust the vulcanization system, especially for rubber products, increase the amount of accelerator; add carbon black for reinforcement or adjust the original formula.
4. If the vulcanization is not familiar, it can be solved by increasing the vulcanization time and increasing the vulcanization temperature; for products with more complex structures, special attention should be paid to the demoulding method to improve the operation level of demoulding workers.
5. Reduce the frequency and dosage of spraying release agent, which can effectively prevent the release agent from polluting the surface of the mold cavity, resulting in difficulty in sticking to the mold.
6. Use a certain amount of release agent.
Keywords:
rubber products
Previous:
Previous:
Recent Posts
CONTACT XIN'AO
Tel: +86-318-5838088
Phone: +86-13703186739
E-mail: sales@xakychina.com
Address: Phase 2, Shuangbed Work Park, Jingzhou Town, Jingxian County, Hengshui City, Hebei Province
Mobile Web
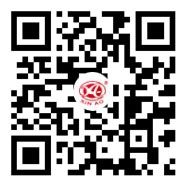
Mobile Web
Copyright © 2022 Hengshui Xin'ao Mining & Metallurgy Rubber Products